05 April 2023
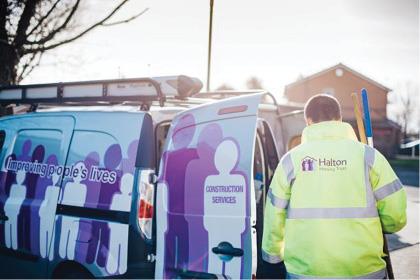
More than 150,000 IoT devices are installed in tenants’ homes by social landlords across the UK. This number is expected to hit 1 million devices by the end of 2024, bringing about a paradigm shift in landlords’ efforts to comply with regulations and offer tenants a better understanding of their home environment.
An increasing number of future-thinking landlords, both social and private, are turning to the IoT for solutions. Smart boilers, connected fire alarms, energy optimisers, air quality sensors, and water leak detectors are the most commonly deployed. Some landlords are also exploring smart locks, advanced assisted living solutions, predictive heating controls and dozens of other technologies.
Councils across the UK are meeting significant challenges in the IoT rollout across housing stock, including poor internet connectivity, operational inertia, and consumer devices being inadequate for multi-property enterprise deployments. There is also a loss of value in not having data in one place for cross-analytics and insight.
Safety first: Halton Housing automates emergency lighting maintenance
Established in Widnes in 2005, Halton Housing is a not-for-profit Housing Association that own and manage over 7,000 homes. Halton Housing has led the charge in technology adoption throughout all sectors of the company with its ‘digital first’ approach. Underpinned by core values of transparency, honesty and innovation, the Halton team have fully embraced digital transformation to help support and improve the lives of their residents.
Automated building compliance
Halton Housing wanted to focus on moving away from manual testing of emergency lighting in their residential housing blocks. Spread out over a wide geographic area, testing of emergency lighting in each block required in-person visits to all lights, at all locations, every month.
Because of the huge number of resources needed to execute testing and maintenance, work was outsourced to a third-party contractor who carried out testing, inspection and repairs on their behalf. PDF certificates of completion were then sent to Halton Housing’s compliance team.
Until then, connecting information to streamline their emergency lighting process was impossible because manual testing gave no indication of failures in advance. Technicians had to attend the site to complete routine testing and determine if there were any problems. If there was an issue with any light the next step was to order the part for replacement and at a later date return to site to complete the repair.
“Our emergency lights which didn’t use LED bulbs failed frequently leading to countless hours wasted going back and forth replacing bulbs,” said Lee Reevell, head of innovation & architecture, Halton Housing. “Another shortcoming we identified in the process was that PDF testing reports generated by our third-party contractor existed in a silo and didn’t feed into any of our inhouse asset management systems.”
After some discussion about the emergency lighting already installed in their buildings and the methods used to test and maintain them, Halton Housing opted to explore alternative options.
Future proofing with IoT
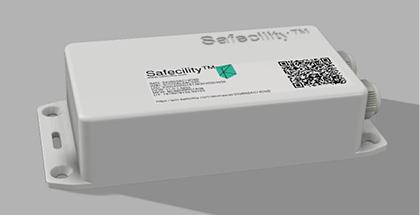
Halton Housing’s journey with Safecility began with a demonstration of Safecility’s Emergency Lighting Controller, leading to an on-site pilot of five devices.
“We’ve big goals when it comes to using IoT to help us pre-empt maintenance in our housing stock,” said Reevell. “We’ve tried a number of different sensors to help us monitor different environmental conditions and also automate compliance testing and improve safety. Many of these sensors work well but can be techy and difficult to set up. Safecility couldn’t be more different - we simply plugged the sensors in and instantly had an automated emergency lighting testing system without any complex set up or extra wiring.”
By taking an active rather than passive approach to emergency lighting, failures are highlighted in real time and remedied quickly.
Automated testing has made managing emergency lighting compliance significantly easier.
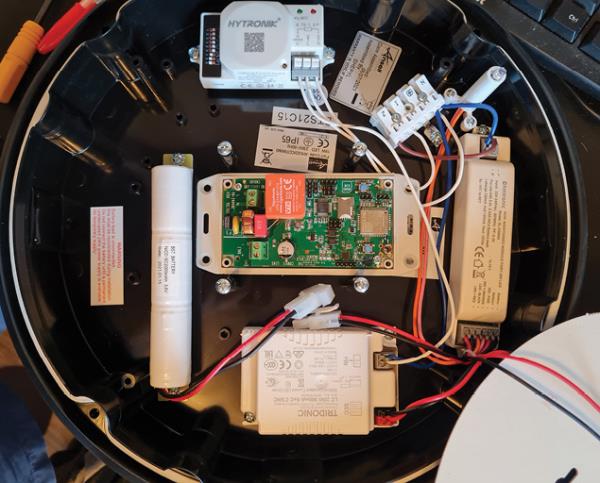
“Safecility’s sensor sends information directly to a software platform where bulb or battery failures are flagged without having to attend the light in person,” said Reevell. “This saves double or triple visits to repair lights and prevents any failures slipping through the cracks. It allows us to be completely confident in the knowledge that nothing has been missed. That we’re fully compliant and our residents are as safe as can be.”
Key benefits of the solution include eliminating unnecessary site visits, the ability to view all pass and failure information for the emergency lighting on a single screen and having full confidence in compliance and safety status.
Safecility is infinitely scalable and can be stored in one building or one thousand, with no extra wiring or gateway installation required.
Other compliance sensor solutions like Legionella monitoring are also available. Results can be streamed directly to the Safecility platform, or via an API to other building management systems.